Sustained Progress: Overcoming Impediments
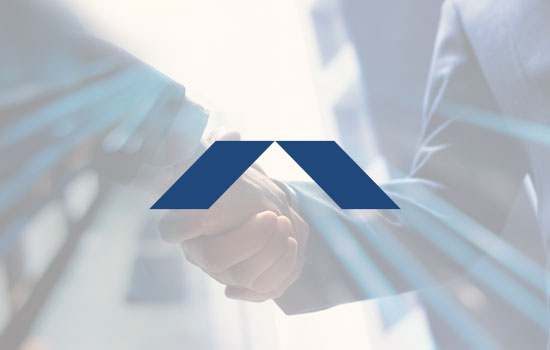
1. Definition of continuous improvement❓❓❓:
Continuous Improvement, also known as “Kaizen,” is an approach based on small, accumulated improvements over a long period. It is a culture and methodology focusing on: Gradual improvement (small but continuous changes), process❓ focus (analyzing current processes to identify weaknesses or opportunities), participation (involving all individuals in the improvement process), and continuous learning (viewing errors as learning opportunities).
2. Scientific Foundations of Continuous Improvement:
Continuous improvement is based on scientific principles:
* Law of Diminishing Returns: Additional efforts initially lead to significant gains, but the benefits decrease over time. Continuous improvement helps maintain returns by focusing on small, accumulating improvements. This law can be represented graphically by a curve that gradually rises and then begins to decline after a certain point.
* Complexity Theory: In complex systems, predicting the outcomes of individual actions is difficult. Continuous improvement allows for small experiments and monitoring of results, helping to understand and adapt❓ to the system with flexibility.
* Deming Cycle (PDCA): A framework consisting of four stages: Plan (identify the problem/opportunity, analyze the current situation, and develop a plan), Do (implement the plan on a small scale or in a test environment), Check (monitor results and evaluate the plan’s effectiveness), and Act (apply the plan on a broader scale or adjust and improve it based on the results). This cycle is repeated to ensure continuous improvement.
3. Importance of Continuous Improvement in Overcoming Obstacles:
Continuous improvement helps: build resilience (adapt to changes), reduce risks (focus on small changes), increase efficiency❓ (reduce waste), and foster innovation (encourage experimentation and learning from errors).
4. Practical Applications of Continuous Improvement:
- Improving Production Processes: Can improve efficiency, reduce defects, and reduce cycle time. For example, “Six Sigma” can identify the causes of differences in product quality.
- Improving Customer Service: Can improve customer experience through feedback collection and analysis.
- Improving Administrative Processes: Can improve efficiency. For example, “Lean Management” can simplify processes and reduce waste.
5. Examples and Related Experiences:
- Toyota: Known for adopting “Kaizen” widely, achieving high levels of quality and efficiency.
- Software Development: “Agile” and “Scrum” methodologies use continuous improvement principles. Large projects are divided into small parts, developed and tested independently.
6. Related Mathematical Formulas and Equations:
Some tools used in continuous improvement rely on mathematical formulas, such as:
- Six Sigma Analysis: Uses statistical tools to analyze data and identify causes of process variations. Standard deviation measures data dispersion around the average: σ = √(Σ(xi - μ)2 / N) where σ = standard deviation, xi = each observation value, μ = arithmetic mean, N = number of observations.
- Key Performance Indicators (KPIs): Used to measure progress, expressed as simple formulas, such as: Conversion Rate = (Number of Conversions / Number of Visits) * 100%.
Chapter Summary
- Obstacles are inevitable and should be viewed as a natural part of the process.
- Fear of failure impedes progress.
- A strong “Big Why” helps overcome obstacles and maintain motivation.
- Failure is not the end but an opportunity❓ for learning.
- “Think Progress” is related to thinking without fear; statistically, increased❓ attempts improve the chances of success.
- Quantity leads to quality, as shown in a ceramics teacher’s study where the group focused on quantity produced higher quality work.
- continuous❓❓ progress is key to overcoming obstacles.
- focusing❓ on the “Big Why” and persisting increases the chances of success.
- Increasing the quantity of attempts leads to experience, skill, and ultimately improved quality.
- Individuals should embrace a growth mindset focused on learning and continuous development.
- Clear and meaningful goals (Big Why) provide the necessary motivation.
- Individuals should adopt an experimental approach, viewing each attempt as a learning opportunity.
- In the early stages, focusing on quantity may be more effective than focusing on quality.